Hazard Recognition and Control

Recognize-Evaluate-Control (REC)
The REC approach to managing hazards is designed to reduce the risk of illness, injury, and death in the workplace. The first step is to survey your farm for potentially hazardous conditions. Here are a few common examples often overlooked.
Recognize - What hazards are present?
Take a walk around the farm and survey the work area(s), equipment, and work-related tasks performed each day, each week, monthly, or occasionally. Look for existing and potential hazards - anything that could result in an injury or illness. A basic checklist is available for use here, a consultant may be available in your area, training may be available either online or in person, or you may rely on the knowledge and experience of farm managers, supervisors, and workers. Examples of hazards on farms include:
- Tractor, mower, or ATV turnover/rollover
- Entanglement (of clothing or hair) from rotating shafts, PTOs, gears, belts, augers, etc. on equipment
- Pinch points or potential crushing from moving parts which could result in an amputation
- Large animal handling - stepped on, kicked, impact or struck by an animal, bites
- Lifting heavy items
- Working from ladders or at heights greater than a few feet
- Slippery walking surfaces, including mud, snow, ice, or manure
- Machinery and equipment such as tractor implements with blades, metal- or wood-working shop equipment
- Use of chain saws for tree trimming or cutting
- Operating heavy equipment such as dump trucks or back hoes where there may be an obstructed view to the rear where other people are working or walking
- Entering confined spaces such as grain storage bins, silos or manure pits where the atmosphere may be hazardous, materials could engulf, drown, or entrap
- Breathing in hazardous chemicals, such as some pesticides or herbicides
- Heat stress or hypothermia from extreme weather conditions
- Working on machinery, equipment, electrical systems or similar where there is a hazardous energy source, such as electricity, compressed air, hydraulics, or even gravity (if working beneath a raised piece of equipment)
- Adverse weather conditions, such as lightning, severe storms, hail, flash flooding
- Exposure to toxins such as nicotine, which can result in Green Tobacco Sickness from handling
For additional information on what OSHA considers to be a hazard in agricultural operations, click here.
Evaluate - What is the risk?
Each hazard should be reviewed to determine the risk involved. Risk refers to the severity of injury (should one occur) and the probability of it happening. A routine (i.e. daily) task that could result in a serious injury or death should be considered "high" risk, where intervention should occur. Where possible, the hazard should be eliminated or properly controlled. Some examples include:
- Climbing a ladder 10-15 feet high where there is no means of fall protection and rungs (or footwear) may be slippery from mud, or attempting to carry tools or materials with you as you climb. A fall from as little as 4 feet could result in an injury where days of work are missed.
- Working around PTOs when cutting hay may only occur during summer months, but getting entangled could result in broken bones, cuts and lacerations, or worse.
- Operating tractors, mowers, ATVs on an incline without rollover protection (ROPS)
Some tasks may only result in minor injuries, and would be considered low risk. Intervention for low risk situations may include minor adjustments or increased awareness and caution when performing the task.
Control - What can be done?
Consider solutions or hazard controls for the high and medium risk situations.
- Can the hazard be eliminated?
- Are there engineering controls that can be incorporated to eliminate access to the hazard, or isolate the hazard from the person?
- What administrative controls can be implemented to increase awareness of the hazard?
- Is there still a risk where personal protective equipment should be worn?
Take a look at the heirarchy of control section below for more ideas on reducing risk to hazards.
Hierarchy of Controls
When evaluating any given hazard, always start with the possibility of eliminating the hazard. Is there a substitution available? Engineering controls isolate or remove the hazard and eliminate or greatly reduce the possibility of exposure. Administrative controls help manage behaviors and procedures that reduce the likelihood of an injury or exposure to a hazard. The purpose of personal protective equipment is to minimize the extent (severity) of the injury.

Elimination of a hazard is completely removing the hazard so that it does not pose an issue. Examples include:
- Getting rid of old machinery or equipment which is not properly guarded, or cannot be guarded for some reason
- Relocating elevated work to ground level so that exposure to a fall is removed
- Backfilling a pit that is no longer used, or filling a groundhog hole so that no one steps in it
- Removing snow, ice, or mud from walking surfaces before work begins
- Eliminating a task or process that may no longer be necessary
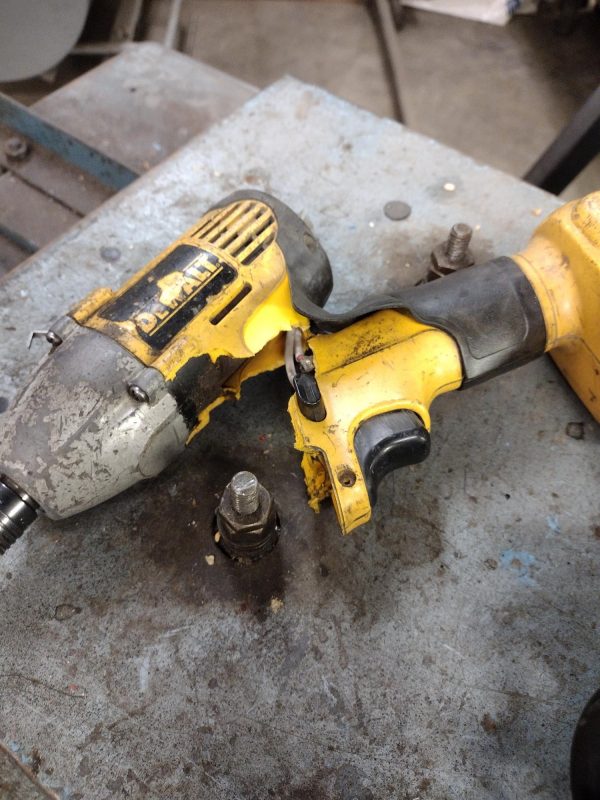
Substitution involves replacing the hazard with a non-hazardous option. Examples include:
- Using water instead of a hazardous chemical for cleaning
- Painting with a brush instead of aerosolized spraying
- Using a less hazardous chemical for a hazardous one
- Automated mixing instead of manual methods
- Bolting two pieces of metal together rather than welding it (which creates a fire hazard, burn hazards, and potential damage to the eyes)

Engineering controls isolate people from the hazard so that injury or illness is not possible. Examples include:
- Machine guarding for power transmission components or at the point of operation (where the work occurs)
- Guardrails or proper work platforms for elevated work locations
- Hole covers on walking surfaces
- Electrical covers on junction boxes and in panels
- Mechanical or natural ventilation in enclosed or confined areas
- Dust collection systems/features on powered tools and machinery
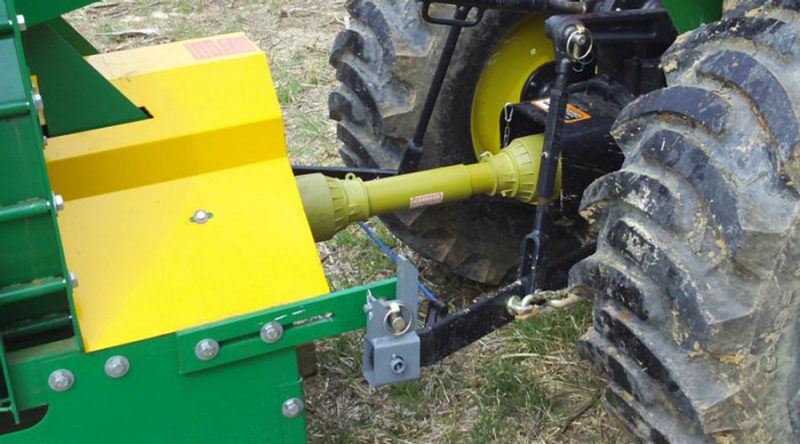
Administrative controls do not remove the hazard, but rather reduce the likelihood of serious injury or exposure by changing the way people work around the hazard. It may not reduce the risk to an acceptable level, and additional means such as personal protective equipment may be necessary. Examples include:
- Reading and following manufacturer's instructions on machinery and equipment
- Use of warning signs or markings such as graphics or color-coding
- Safe work practices or procedures (ex. ladder safety, animal handling)
- Audible backup alarms on heavy equipment
- Maintaining safe distances from the hazard (3-feet is a good rule-of-thumb)
- De-energize and secure any hazardous energy source before performing servicing/maintenance activities or entering confined spaces
- Check the air before entering confined spaces
- Frequent breaks to rest, hydrate, cool off or get warm from extreme weather conditions
- Adjusting work hours to early morning or night-time when it's cooler to avoid heat stress
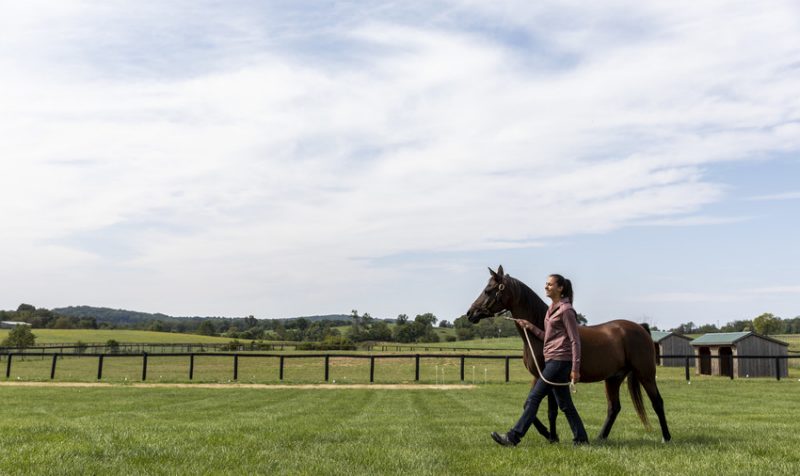
Personal protective equipment (PPE) protects the worker from the hazard and/or minimizes the severity of injury or exposure. It is worn by the worker, and the degree of protectiveness can vary due to factors such as proper use, cleaning, maintenance, or design limitations. It must be properly selected based on the hazards identified. Examples include:
- Protective headwear (ex. helmets, hats with a brim)
- Safety glasses or goggles
- Face shields or welding helmets/goggles
- Respirators (ex. N-95) or simple dust masks
- Flame-retardant jackets or sleeves for welding activities
- Various types of gloves (i.e. hazard-specific)
- Chaps for chain saw use or animal handling
- Sin guards or knee pads
- High-visibiltity shirts, vests, or jackets
- Slip-resistant footwear or steel-toed boots
- Use of seatbelts
- Sunscreen
- Chemical-protective clothing for pesticide application
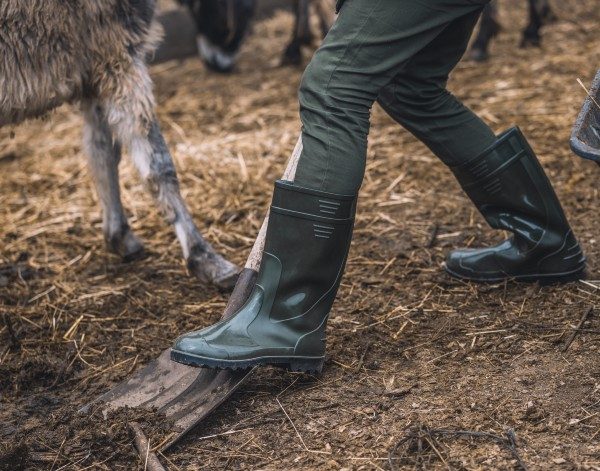
All serious hazards should be addressed immediately. Avoid selecting controls that may directly or indirectly introduce new hazards. Examples include exhausting contaminated air into occupied work spaces, or using hearing protection that makes it difficult to hear backup alarms.
Managing the risks associated with your work is a shared responsibility. Involve workers who are using the machinery/equipment or performing the task to help identify hazards, and offer solutions. Regulations, laws, training, and workplace policies are only a small part of what makes a workplace safe. We encourage each of you to be innovative as you work with each other, your supervisors, and senior managers to create a safe and healthful workplace. Ask questions, talk openly, and share your ideas and solutions with each other.