Module 3: Hazardous Chemicals
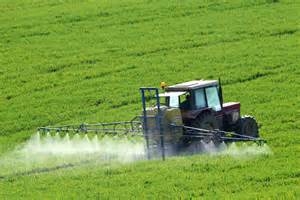
Various forms of chemical hazards exisit on farms. From fertilizers, pesticides, and cleaning solutions, there is always a chance of exposure to some sort of chemical on a farm. Understanding the hazards the chemicals pose is critical. This module is set to help you understand the steps your employer is required to take to ensure you have a safe operation.
When does a chemical become a hazard?
A chemical can become a hazard to you when you do not follow the manufacturers instruction, when you have abnormal conditions, you make a mistake, equipment fails, or some other unusal event such as a power outage.
Recognizing the Hazard
How do you recognize the hazard?
The Hazard Communication Program provides us five key pieces:
- A written Hazard Communication Plan (HazCom)
- Labeling
- Safety Data Sheets (SDS)
- Training
- Chemical Inventory list
Hazard Communication Plan
The written HazCom plan is developed to identify and alert employees to the hazards posed by the chemical they are exposed at work. Even if they do not handle the chemical directly, if they can be exposed to the chemical, they need to be aware.
Labeling
Labels can provide you a lot of information. Labels communicate the hazards through the use of Signal Words, Hazards Statements, Precautionary Statements, and Pictograms. All containers must be labeled. If a label is missing, you should make a new one for the container.
Signal Words
- Danger, you know you should be handling this with a little more care.
- Warning is used to identify a chemical with a lower hazard potential, but still requires some attention.
Hazard Statements
Ususally a short comment on the hazard. (Ex. Causes serious eye damage.)
Precautionary Statement
These provide inforamtion to minimize or prevent adverse effects. (Ex. Avoid breathing fumes/mists/vapors/spray.)
Pictograms
Represent the hazard classification of the chemical.
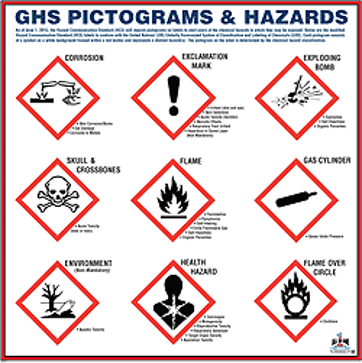
A Word About Labels
Using the Global Harmonization System (GHS) has led to confusion. Many employers have used the NFPA “fire diamond”, and the HMIS rating system to rate chemical hazards. These systems use a number to tell you how hazardous a chemical is. Higher numbers indicating a bigger hazard. The new GHS / OSHA rating system is the reverse; the lower the number the higher the hazard.
You must know whether the label is an “old” HMIS/NFPA label or a “new” GHS label!
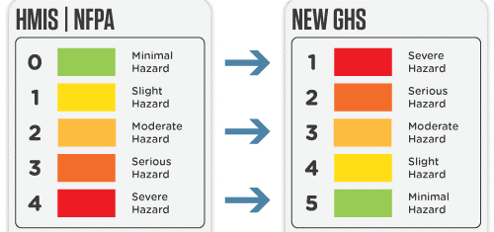
Secondary Containers
If you move a chemical from the original container to a secondary container, the secondary container should be labeled with a GHS-compliant label.
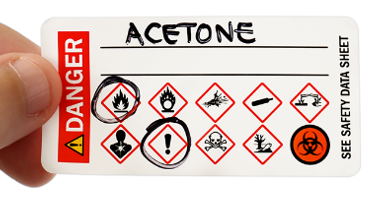
** When you move a chemical to a temporary container, a label isn’t required as long as the temporary container remains in your possession and is used promptly.**
The Safety Data Sheet (SDS)
The SDS is developed by the manufacturer or importer to provide you with all the information on the particular chemical. These should be kept on site in a location that all employees have access to.
There are 16 Sections, the first 8 are the ones you really need to be familiar with if you use the chemical.
- 1- Chemical Identifier
- 2- Hazard(s) Identification
- 3- Composition/Ingredients
- 4- First Aid
- 5- Fire Fighting Measures
- 6- Accidental Release
- 7- Handling and Storage
- 8- Exposure Control/PPE
The second half of the SDS is no less important, and should be reviewed before using the chemical, mixing with other chemicals, disposing of the chemical, and transporting to other locations.
- 9- Physical and Chemical Properties
- 10- Stability and Reactivity
- 11- Toxicological Information
- 12- Ecological Information
- 13- Disposal Considerations
- 14- Transport Information
- 15- Regulatory Information
- 16- Other Information
Training
The HazCom Standard requires employers to provide training to employees. That training must cover:
- The specifics of the company HazCom Plan and where it is located (Usually kept with the SDSs).
- Information about the specific chemicals you work with or have in your work areas.
- How to work safely with or around those chemicals.
- Location of SDSs.
- Understanding how to detect or react to a leak of a chemical.
- How to protect yourself from the hazards of a chemical.
Chemical Inventory
Employers are required to maintain a list of all chemicals used in the workplace. Employers must record the product names of all chemicals, using a name that can easily be matched to the Safety Data Sheet.
Hazard Controls
Your employer has additional tools to help keep you safe. Understanding how to RECOGNIZE the hazard, EVALUATE the hazard, and CONTROL the hazard is a critical path to follow.
RECOGNIZE
- The tasks you’re asked to perform;
- The equipment you’re asked to use;
- How you’re expected to perform work tasks; and
- Where you perform work / use equipment.
EVALUATE
- Safety of the chemical.
- Potential health affects.
- Any personal risk factors.
CONTROL
- Train employees on the chemicals being used.
- Use chemicals properly.
- Try engineering and administrative controls first.
- Use PPE when other control methods are not possible.
Understanding the Hierarchy of Controls
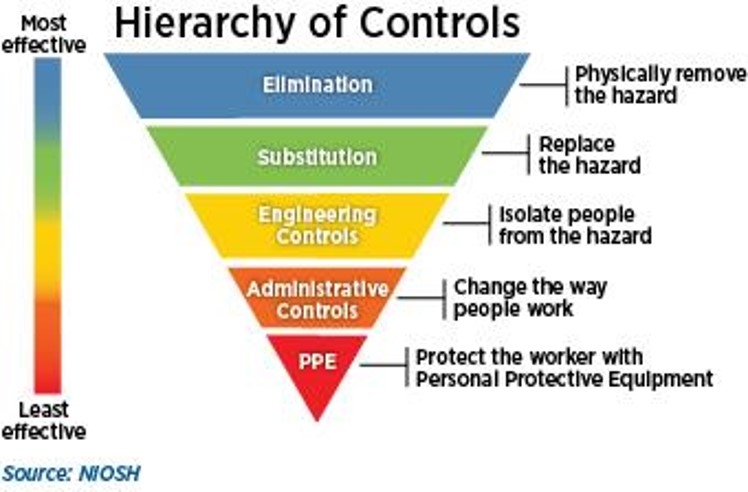
Engineering Controls remove the hazard from the workplace or use a barrier to virtually eliminate worker exposure to a hazard. The hazard is controlled on a relatively permanent basis. Engineering controls are the most desirable and effective type of hazard control, but may not always be feasible due to time and money constraints.
Administrative Controls change how you do something. In cases such as fueling, how you perform a task can impact the risk the hazard presents to you. When you follow administrative controls such as signage, you make the task safer even though the hazard is still there. In some cases, you may still have to use personal protective equipment (PPE).
Personal Protective Equipment reduces your risk through the use of safety eyewear, gloves, shoes, face shields, specialized clothing and respirators. PPE does not eliminate the hazard, but can reduce the seriousness of injury or illness if an exposure occurs. PPE is used when all other controls cannot completely control the hazard.
About PPE
PPE is your last line of defense against hazards that cannot be completely managed or removed by other control mechanisms. The selection and requirements for your use of PPE is based on the specific hazards you encounter while doing your job. PPE, with some exceptions for footwear and eyewear, must be provided to you by your employer for free.
PPE normally considered when using hazardous chemicals:
- Gloves
- EyeProtection
- FaceProtection
- Bodywear
- Slip Resistant Footwear
Gloves - an integral part of any work with hazardous chemicals. Different chemicals may require you to wear different types of gloves. Gloves can provide protection from chemicals, cuts, heat / cold exposure, and electrical hazards.
Appropriate Use of Gloves
- Use disposable gloves whenever possible.
- Gloves must be appropriate for the task and chemical products you are using.
- Remove gloves after completing a task in which they become contaminated. Don’t use the same pair of gloves with multiple chemical products.
- Never wear potentially contaminated gloves into a public area.
- Handle clean items with clean gloves.
- Change gloves frequently if needed, washing your hands between.
- Wash your hands after removing gloves and when changing gloves.
- Hand sanitizer is useful, but not a substitute for hand washing. Even if you use hand sanitizer, wash your hands when possible.
How do you wash your hands?
Eye and Face Protection includes Safety Glasses or Goggles to prevent chemical splash, projectiles and other debris from hitting the eye as well as Face Shields which provide extended protection for those same types of hazards to your whole face, and are used in conjunction with safety glasses or goggles.
Bodywear includes such items as long pants and a long-sleeve shirt. Some work tasks may require additional bodywear to protect you from chemicals you may be using. These items may include aprons or coats, coveralls, or coated sleeves.
Footwear is an important part of your PPE. As with all other PPE, the specific requirements are based on the hazards in your workplace. Footwear can be used to prevent slips, trips and falls, protect from chemicals spilled, or protect from dropped objects.
BEST PRACTICES
Storing Chemicals
- Keep storage areas neat and orderly.
- Store chemicals in a designated areas.
- Store like chemicals together.
- Keep an inventory.
- Use proper containers for storage.
Handling Chemicals
- Automate mixing and dispensing of chemicals whenever possible.
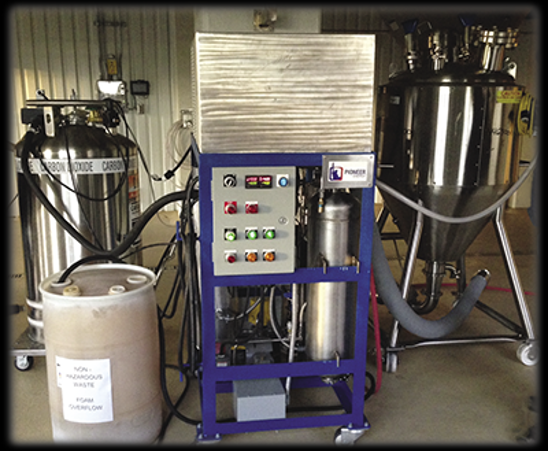
- When mixing by hand, follow procedures and work slowly and deliberately.
- Rely ONLY on product labels or instruction sheets when preparing and mixing product.
- Follow mixing guidelines exactly.
- Use premixed chemicals or fuels when feasible.
- DO NOT rely on product coloration to determine the products or mixtures.
- Use care when transferring chemicals from bulk containers.
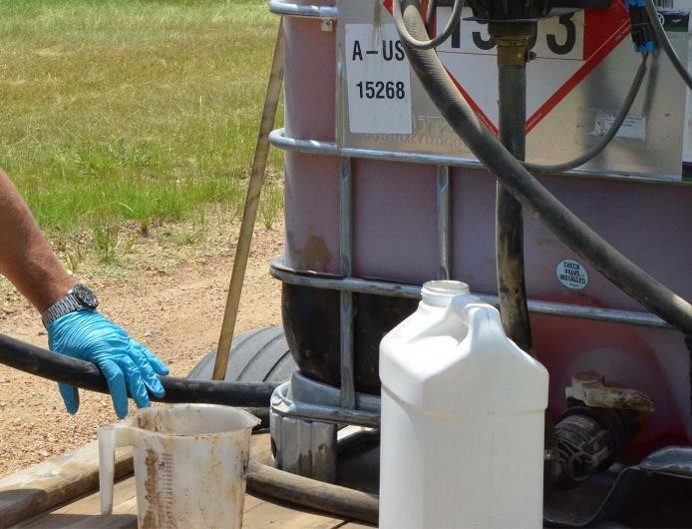
- Ensure all connections are secure.
- Wear appropriate PPE as outlined in the SDS.
- When possible, use the labels supplied by your chemical supplier on secondary containers.
- Secondary containers must have GHS-style labels unless exempt.
- Do NOT use food product containers as secondary containers.
Using Chemicals
- Wash your hands after removing your gloves when you’ve handled hazardous chemicals.
- Never eat or drink, apply cosmetics, smoke, or handle contact lenses when handling or using chemicals.
- Use chemicals only for their intended purpose.
- Don’t make assumptions based on containers, colors, or past experiences.
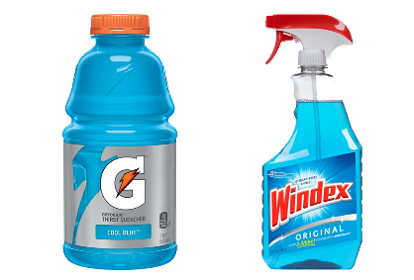
- Use only approved bottles or packages as secondary containers.
Spills and Emergency Steps
For small spills, it may be okay to clean up on your own. Follow the spill guidlines provided by your employer in the HazCom plan. Check the SDS also.
Otherwise, your first priority is your own health and safety.
- Leave the area and warn others.
- Inform appropriate personnel, including 9-1-1 if indicated;
- Assist others with leaving the area and assist with shutdown if safe;
- Do not return to a spill area until it is safe to do so.
Getting Help - Call 911 or local resuce, know your location, and work in groups of two or more.
Until Help Arrives - Ensure your own safety, gather known information on the exposure, follow instructions of dispatcher, and provide basic first aid if trained.