Hazard Communication Program
Hazard Communication Planning Quick Links
Hazard Communication Overview
Personnel whose chemical use is limited to consumer or commercial chemicals/chemical products are subject to the Hazard Communication Program at Virginia Tech.
(Personnel who use scientific-grade hazardous chemicals/gases and "laboratory-scale" quantities in laboratory research are regulated differently).
Virginia Tech’s Hazard Communication Program has been prepared in accordance with the requirements of the OSHA Hazard Communication Standard, 29 CFR 1910.1200. OSHA requires manufacturers and importers to evaluate their hazardous chemicals for physical and health hazards and to communicate specific hazard information to downstream chemical users. OSHA also requires employers to both ensure hazard information is available to employees, and train their employees to understand and use hazard communication in order to work safely.
Virginia Tech departments will accomplish the safety goals of the OSHA Hazard Communication Standard for their employees, personnel, and students in the following ways:
Ensure that the following information is available to personnel on workplace-specific chemical hazards:
- Labels and other forms of warning on chemical and chemical product containers;
- Safety data sheets (SDS); and
- Employee information and training.
Hazard Communication Online Program
Hazardous chemicals: Hazardous chemicals implies that exposure to a chemical could pose a physical and/or health hazard. Physical hazard indicates that the chemical is a combustible liquid, a compressed gas, explosive, flammable, an organic peroxide, an oxidizer, pyrophoric, unstable (reactive), or water-reactive. Health hazard indicates that acute or chronic health effects may occur in exposed employees.
Exempt chemicals: Common exemption - If you are using a consumer product in the same size container you would use at home, in same way/in same quantity you would use the product at home, the Hazard Communication Standard does not apply. However, if you are using multiple containers or bulk-volume containers of the product for a task, or are using the product for any purpose or in any way other than as described on the label, the standard would apply. Certain chemicals are specifically exempt from this Hazard Communication Program, including pesticides, fungicides, rodenticides, food, food additives, drugs, cosmetics, and medical or veterinary products. A more complete list is provided in the OSHA standard 1910.1200 (b)(6).
Department management bears the responsibility for providing Hazard Communication Program resources to supervisors who oversee work areas and manage personnel and hazardous communication coordinators who facilitate safe chemical use in the workplace. In some instances, a supervisor may also serve as the hazardous communication coordinator. Department management also is responsible for ensuring that hazard communication training records for personnel are up-to-date and maintained in department files and/or the Environmental Health & Safety Safety Management System.
Hazard communication coordinators are responsible for executing the requirements of this program so that all persons safely work with hazardous chemical products in their work areas.
Responsibilities include:
- Required training: Complete Hazard Communication and Hazard Communication Coordinator Training.
- Chemical inventory: Develop and maintain an inventory list of all hazardous chemicals stored or used in the workplace, ensure the inventory is available to employees (see Hazard Communication Chemical List Template), and ensure that chemical containers are properly labeled.
- Safety data sheets: Ensure safety data sheets are present for all hazardous chemicals and chemical products in the workplace and readily available to employees.
- Hazard communication plan checklist and annual review: Complete this template to capture department/area-specific details.
- Non-routine task awareness: Identify non-routine tasks involving hazardous chemicals. Ensure written standard operating procedures are established and included in department-specific training for employees performing non-routine tasks involving hazardous chemicals.
- Retain the completed form in the hazard communication plan binder, along with other required elements of your plan.
- Review and update your hazard communication plan contents as necessary and at least annually.
Employees must:
- Comply with the guidelines set forth in this program and in the department-specific hazard communication plan.
- Complete required Hazard Communication Training.
- Following training, know how to recognize hazards associated with chemical products, and use chemical products safely.
Contract employees are responsible for:
- Complying with this plan in accordance with the Virginia Tech Contractor Safety Guide.
Environmental Health and Safety will:
- Maintain and update this written hazard communication plan and the plan templates for departmental use, as well as provide assistance when necessary and requested. Environmental Health & Safety will provide online Hazard Communication Training and Hazard Communication Coordinator Training for use by personnel at Virginia Tech.
- A hazard communication plan is required for each workplace that is subject to the requirements of the Hazard Communication Program (i.e., for workplaces that are NOT research laboratories using scientific-grade hazardous chemicals/gases).
- The required elements of a hazard communication plan include:
- Hazardous chemical inventory/list;
- Safety data sheets; and
- Hazard communication plan checklist and annual review.
- A department/work area’s hazard communication coordinator:
- Develops a hazardous chemical inventory or list for their work area;
- Compiles safety data sheets for those hazardous chemicals;
- Completes the template for the hazard communication plan checklist and annual review; and
- Places all of this material (which is now that work area’s hazard communication plan) in a binder, and locate the binder in the workplace where it is accessible to personnel.
- Recommendation: Print out the Hazard Communication Program document and include it in your hazard communication binder for ready reference, especially if your computer access to the program document is limited/not available.
- Each Virginia Tech department, facility, or workplace for which the Environmental Health & Safety Hazard Communications Program applies must list or inventory all hazardous chemicals in the workplace. This list includes the name of the chemical and the specific work area in which the chemical is used, or the person responsible for the chemical. Refer to the Hazard Communication Chemical List Template.
- The hazardous chemical inventory or list is compiled and maintained by the hazard communication program coordinator or departmental designee.
- This list shall be retained with the designated hazard communication program documentation (binder) in the workspace.
- When new chemicals are received, this list must be updated (including date the chemical was put into use). To ensure any new chemical is added in a timely manner, the following procedures should be followed:
- If the chemical is ordered by any individual other than the hazard communication program coordinator, they must notify the coordinator of all chemicals ordered, including the following:
- The date the order was placed;
- The name of the chemical and manufacturer;
- The specific work area in which the chemical will be used;
- The quantity to be used; and
- The expected receipt date.
- When a shipment arrives, the receiving department must notify the hazard communication program coordinator immediately and deliver the new safety data sheets and any additional information on the chemical provided with shipment to the coordinator.
- The hazard communication program coordinator must then add new chemicals to the list with all required information. An updated copy of the list must then be attached to the workspace-specific hazard communication program documentation and the old list destroyed.
- If the chemical is ordered by any individual other than the hazard communication program coordinator, they must notify the coordinator of all chemicals ordered, including the following:
- What are safety data sheets?
- Safety data sheets are documents (paper or electronic) supplied by manufacturers which provide product users with detailed information on hazardous chemicals.
- Information found in safety data sheet documents includes, but is not limited to, the product name, chemical abstract service numbers, composition, handling precautions, type of personal protective equipment recommended, physical and health hazards, storage requirements, emergency, and first aid procedures, the date the safety data sheet was prepared, name, address and telephone number of the chemical manufacturer or the importer. See table below for safety data sheet information, section by section.
- Employers must ensure that safety data sheets are readily accessible to employees.
- For details about each section, see OSHA's Brief safety data sheets.
- Where do I find safety data sheets for the products used in my workplace?
- Safety data sheets must be available for each hazardous chemical or chemical product used and must be readily accessible to employees. You should be informed of the location of the safety data sheet when you begin working in your area. All employees should review safety data sheet documents prior to using hazardous chemicals.
- The hazard communication coordinator or designee is responsible for obtaining safety data sheet documents for the department when new chemicals are procured. This person also reviews incoming safety data sheet documents for safety and health information to convey pertinent information and training to affected employees.
Section 1 | Identification of Product | Product identifier; manufacturer or distributor name, address, phone #; emergency phone #; recommended use; restrictions on use. |
Section 2 | Hazards Identification | All hazards regarding the chemical; required labeling elements. |
Section 3 | Composition/ Ingredients | Information on chemical ingredients; trade secret claims. |
Section 4 | First Aid Measures | Important symptoms/effects, acute, delayed; required treatment. |
Section 5 | Fire-Fighting Measures | Suitable extinguishing techniques, equipment; chemical hazards from fire. |
Section 6 | Accidental Release Measures | Emergency procedures; protective equipment; proper methods of containment and cleanup. |
Section 7 | Handling and Storage | Precautions for safe handling and storage, including incompatibilities. |
Section 8 | Exposure Controls/Personal Protection | Exposure limits used/recommended by manufacturer/importer, engineering controls and personal protective equipment. |
Section 9 | Physical/ Chemical Properties | Chemical’s characteristics. |
Section 10 | Stability and Reactivity | Chemical stability and possibility of hazardous reactions. |
Section 11 | Toxicity Information | Routes of exposure; related symptoms, acute and chronic effects; numerical measures of toxicity. |
Section 12 | Ecological Information | Other Agencies regulate this information; OSHA does not enforce Sections 12 through 15 (29 CFR 1910.1200(g)(2)). |
Section 13 | Disposal Considerations | |
Section 14 | Transport Information | |
Section 15 | Regulatory Information | |
Section 16 | Other Information | The date of preparation or last revision. |
The hazard communication coordinator or designee shall ensure primary and secondary hazardous chemical containers are properly labeled. All labels and warnings should be legible, written in English, and prominently displayed on the container.
Primary or original manufacturer’s labels
Chemical manufacturers, importers, or distributors are required by OSHA to label, tag, or mark each container of hazardous chemicals with the following label elements after they classify the hazards of the chemical. Virginia Tech employees must understand how to read and follow chemical labels. Each label has five key elements in addition to manufacture information:
- Name, address, and telephone number of the chemical manufacturer, importer, or another responsible party.
- Product identifier (how the hazardous chemical is identified) can be (but is not limited to) the chemical name, code number, or batch number. The manufacturer, importer, or distributor can decide the appropriate product identifier. The same product identifier is found both on the label and in section 1 of the safety data sheet for any given chemical.
- Signal words alert the reader to the relative severity of the hazard posed by that chemical. There are only two words used as signal words, "Danger" and "Warning." Within a specific hazard class, "Danger" indicates a more severe level of hazard, and "Warning" indicates a less severe level of hazard. There will only be one signal word on the label no matter how many hazards a chemical may have. If a chemical has more than one hazard and one of the hazards warrants a "Danger" signal word, then "Danger" should appear on the label, even if its other hazards warrant the "Warning" signal word.
- Pictograms are graphic symbols used to communicate specific information about the hazards of a chemical. OSHA requires chemical hazards to be conveyed via pictograms on primary labels. Each pictogram is determined by the specific OSHA hazard classification(s). See OSHA’s nine pictograms and corresponding hazards in the following table below.
- Hazard statements describe the nature of the hazard(s) of a chemical, including, where appropriate, the degree of hazard. For example, "Causes damage to kidneys through prolonged or repeated exposure when absorbed through the skin." The hazard statements are specific to the hazard classification categories, and chemical users should always see the same statement for the same hazards no matter what the chemical is or who produces it.
- Precautionary statements describe recommended measures to minimize or prevent adverse effects resulting from exposure to the hazardous chemical or improper storage or handling. There are four types of precautionary statements:
- Prevention (to minimize exposure);
- Response (in case of accidental spillage or exposure, emergency response, and first aid);
- Storage; and
- Disposal.
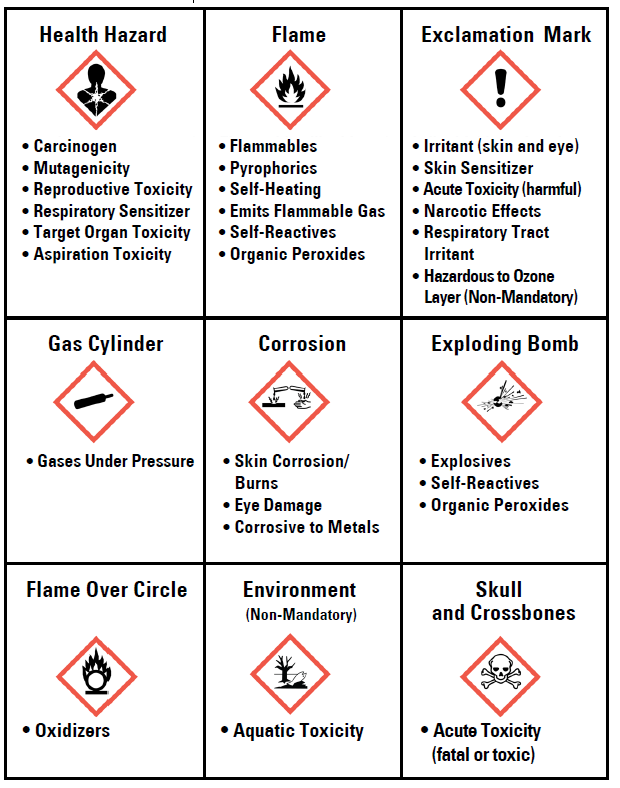
Labels on incoming containers must not be defaced or removed until the container is empty. If the label becomes faded, illegible or destroyed they should be replaced and remain durable, legible, and firmly affixed to the container(s).
The example label depicts the use of all labeling elements:
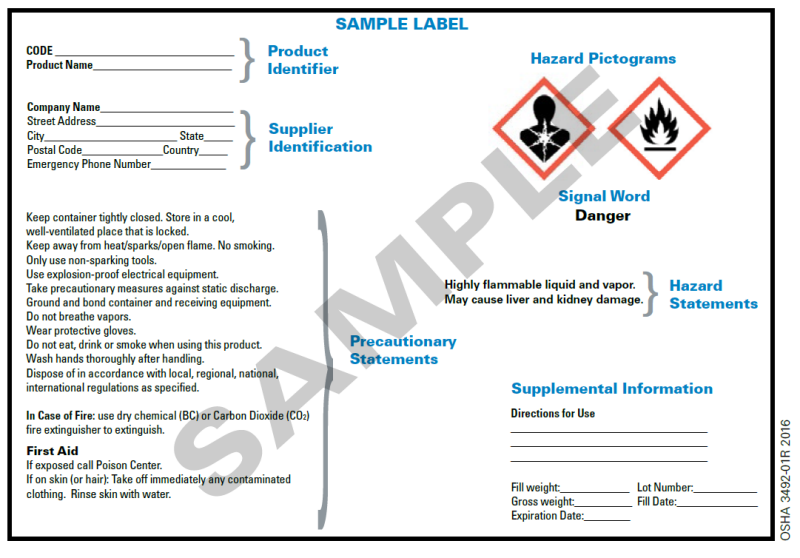
Secondary or alternative labeling
The following guidelines summarize the secondary or alternate labeling options available:
- Creating your own container labels:
- The full chemical or product name(s) (as it appears on the safety data sheet) and the primary or general hazard can be written directly on the container or written/printed on a label to be affixed to the container.
- For common chemicals/chemical products, you can use:
- An abbreviation or trade name that is commonly used and easily recognized.
- A standard chemical formula (not structural formula) that is commonly used and easily recognized.
- Always include the primary or general hazard, (FLAMMABLE, for example) which can be written directly on the container, or written/printed on a label to be affixed to the container.
- If a container is too small or the identity name is too large, a codified name may be used on the container when defined in a notebook or reference sheet that is accessible to all. When many chemical names are needed, readily accessible notebook references may be used and primary hazards must also be communicated in the notebook or in the general workspace using words, symbols, or pictograms.
- You can even include the five label elements as used on primary labels. However, secondary workplace container labels do not require the inclusion of the five label elements.
- The primary or general hazards can be placed on container labels using words, pictures, symbols, or a combination of these that provide general information about the hazards of the chemical.
- For common chemicals/chemical products, you can use:
- Using existing workplace container labeling systems:
- Examples: National Fire Protection Association (NFPA) or Hazardous Materials Identification System (HMIS); the new Globally Harmonized System of Classification and Labeling (GHS) is also available.
- Any rating system can continue to be used as long as employees have immediate access to the specific hazard information (typically via safety data sheet or container labels) associated with the hazardous material(s). Task-specific training must be provided to ensure that all employees are fully aware of the hazards of the chemicals used, and how to correctly interpret the hazard rating system in use.
- IMPORTANT: Note that the hazard severity ranking within the NFPA and HMIS systems is opposite from the newer OSHA hazard classification severity rankings. NFPA diamonds and HMIS labels range from 0 to 4 where 4 is the most severe. These labels use general hazard groups (flammable, health hazard, and reactivity or physical hazard). OSHA hazard classification rankings use 1 as the most severe category of given hazard classification and are more specific hazards.
- Secondary labeling requirements:
- Every label must convey the required information clearly, legibly, and in English. Where other languages are spoken in the work area, information may be presented on labels in other languages in addition to the required English words. Virginia Tech does not mandate any single labeling system.
- There are currently many labeling (marking) systems in use. The best programs utilize a simple system that is readily recognizable and easily understood. Any worker should be able to quickly identify the general hazard of material and the severity of the hazard by glancing at the label.
- The full chemical or product name(s) (as it appears on the safety data sheet) and the primary or general hazard can be written directly on the container or written/printed on a label to be affixed to the container.
Transfer containers
- When hazardous chemicals are transferred from a labeled container to a portable container that is only intended for immediate use by the individual who performs the transfer, no labels are required for the portable container. However, it is best practice to always label secondary containers in the event the user is distracted or a spill occurs. Labeling will eliminate confusion where there are more than one (unlabeled) container in use, and ensure that container content is known in the event of an emergency where outside personnel may be involved.
- Transfer container labeling must include the name of the substance and hazard warnings in a manner consistent with your work area established alternative workplace labeling system.
- What is a non-routine task?
- A non-routine task is one which the employee does not normally perform and for which he/she has not previously been trained.
- What needs to be in place before employees perform non-routine tasks?
- Standard operating procedures should be written and available to employees performing "non-routine" tasks involving hazardous chemicals.
- Prior to beginning non-routine tasks involving actual or potential exposures to hazardous chemicals, employees should be informed of the hazards present, and the steps the department/ work area is taking to reduce the hazards, including ventilation, respirators, the presence of another employee (buddy systems), and emergency procedures.
- The employee should be given appropriate work instructions, and provided with required personal protective equipment prior to starting the task.
- Who is responsible for putting these measures in place?
- The employee’s supervisor or the area supervisors are responsible for standard operating procedure development, supplying personal protective equipment and providing information and training.
The presence of hazardous chemicals in the work environment can typically be detected by visual appearance or odor of the hazardous chemical being released. If such releases are identified (and not planned), contact your supervisor immediately and evacuate the work area in accordance with your department’s Emergency Action Plan as appropriate.
Hazardous chemicals can also be detected through air monitoring when there is no visible indication of a spill or odors cannot be used as indicators of releases. Virginia Tech Environmental Health & Safety may conduct air monitoring as needed basis to determine whether an OSHA Permissible Exposure Limit or Equivalent Threshold (usually found in a safety data sheet, if available) has been exceeded. Environmental Health & Safety will then determine the necessary personal protective equipment and engineering controls to be used.
- What training is required for personnel and students who use consumer or commercial chemicals/ chemical products in the workplace?
- Complete Environmental Health & Safety's online Hazard Communication (HAZCOM RTK) Training.
- Workplace-specific information on chemicals/products used and associated hazards, required personal protective equipment, and safe work practices must be provided to new personnel by the work area supervisor. Some of this information will also be conveyed by the hazard communication coordinator when he/she reviews the hazard communication plan with each new employee.
- Additional workspace-specific training on hazards must be provided by the department and or work area supervisor whenever a new hazardous chemical/chemical product that is introduced into the workspace. Records of this additional training shall be maintained by the hazard communication program coordinator.
- What should I learn in Hazard Communication Training (online and workplace-specific)?
- The requirements of the Hazard Communication Standard (29 CFR 1910.1200).
- The contents, location and availability of my workplace hazard communication plan.
- The physical and health hazards of hazardous chemicals in my work area and their locations.
- The location of my work area’s hazardous chemicals inventory list.
- The location of safety data sheet documents for all hazardous chemicals in my work area, and how to find/understand the hazard information from them that I could need.
- How to properly label containers, and understand workplace labels/ labeling systems and other forms of warning.
- The emergency procedures to follow related to chemical hazards.
- The methods used to determine the presence or release of hazardous chemicals in the work area.
- How to reduce or prevent exposure to hazardous chemicals by using good work practices, engineering controls and personal protective equipment
- What training is required for hazard communication coordinators?
- All individuals who will serve as hazard communication coordinators must successfully complete the Environmental Health & Safety online module for HazCom Coordinator Training. Training will include topics covered in basic Hazard Communication Training, as well as a review of coordinator responsibilities.
The Hazard Communication Program will be reviewed by the Environmental Health & Safety Hazard Communication Program administrator annually and updated as necessary.
In addition, each department's hazard communication program coordinator is responsible for annual review/revision of their department's or workplace's completed hazard communication plan checklist and annual review. The hazard communication plan is subject to Environmental Health & Safety review during safety evaluations.
Last review: March 5, 2017
Frequently Asked Questions
Virginia Tech Pesticide Programs (VTPP) provide pesticide safety information, training, and educational resources to pesticide applicators, Extension agents, and the public.
In addition, the Office of Pesticide Programs under Virginia Department of Agriculture and Consumer Services (VDACS) provides certification and registration services.
"We have a large 'cardboard box' type of container for broken glass that is full and needs to be removed. Who do we ask or who would be in charge of this service?"
There are a couple of options:
- If the box only contains broken glass or bottles with defaced labels that are not contaminated with any hazardous material, and does not contain any empty containers of an EPA P- listed material: tape up the box and put it in the nearest dumpster. Housekeepers/custodial staff, have been instructed not to pick up any ‘broken glass’ boxes.
- If the box contains broken glass that is or may be contaminated with any hazardous material and/or empty containers of an EPA P- listed material, the waste must be managed by Environmental Health & Safety. For a pickup, please submit a completed waste label per the Chemical Waste Disposal Procedures.
The Virginia Tech chemical hygiene plan is included as part of the Chemical Safety Program. The chemical hygiene plan is designed to be reviewed online, but a paper copy can be obtained using the printer-friendly link provided.
The Laboratory Requirements section includes reference information and a link to the Laboratory-Specific document. Formerly known as Part B of the CHP, this Laboratory-Specific documentation must be completed and maintained on file for all chemical/biological laboratories.
The Hazard Communication Standard, 29 CFR 1910.1200(g), was recently revised to change the former material safety data sheet (MSDS) to a more consistent, user-friendly format. The new form is called a safety data sheet (SDS).
Details on verifying the format of your safety data sheet are available to download.
Please refer to this document for guidance in obtaining safety data sheets for either new chemicals or to replace older material safety data sheet format.
Environmental Health & Safety reviews refrigerator and freezer purchases to ensure the appropriate types of refrigeration units are being acquired for use in laboratories. Volatile solvents and flammables must not be stored in the unit on sale at Home Depot or Lowes. Purchases must be approved by Environmental Health & Safety.
Environmental Health & Safety reviews requests based on the following criteria.
1) Is this purchase for a non-laboratory / chemical use group? For example, student housing, we approve the request immediately and the order proceeds through HokieMart.
2) If this purchase is for a laboratory/chemical use group, then Environmental Health & Safety will ask:
- Is the refrigerator flammable storage rated?
- Is the freezer-unit a manual defrost?
- Is this a laboratory-rated refrigerator or household unit?
The questions must be answered before approval can be given. Environmental Health & Safety makes every effort to facilitate Virginia Tech research efforts in ensuring the safety of our campus.
Contact Autumn Timpano with Environmental Health & Safety at 540-231-3247 for further information.
Handling and storage requirements vary based on the flammable or combustible classification of a material. Please refer to the Hazardous Chemicals section of the Fire and Life Program for further details.
Because many fluorescent light tubes contain mercury, a program has been established to dispose of the light tubes according to local, state, and federal regulations. We ask that all discarded tubes be placed in a cardboard box and labeled with a hazardous waste label. Please see chemical waste disposal procedures for details.
Light ballasts and transformer oil may contain PCBs (polychlorinated biphenyls) which are regulated hazardous waste. Before disposing of light ballasts or recycling transformer oil, please contact 540-231-3600 so we may test the materials for PCBs.
A general checklist for reviewing chemical/hazardous waste collection in laboratories and other work areas. If you have questions, please contact:
- Hazardous Materials Program Manager Kenny Osborne at kosborne@vt.edu;
- Chemical hygiene officer at 540-231-3427; or
- Or Environmental Health & Safety at 540-231-3600.
Chemical manufacturers and importers must evaluate their products to determine if they are hazardous. For those materials so designated, a safety data sheet (SDS) (formerly known as a material safety data sheet or MSDS) must be sent to those who purchase the items. In addition, the manufacturers are responsible for updating the safety data sheet if product information changes. Each department or work area must maintain a safety data sheet for each hazardous chemical/product they use and safety data sheets must be readily available to all using the materials. Electronic systems may be used but only if emergency back-up is supported in cases of power and/or equipment failure.
Please refer to Safety Data Sheets for more information.
Employees in retail sales or warehousing, for example, must receive training on what to do if there is a spill or leak of the container, and safety data sheets formerly known as material safety data sheets must be available for review. Employees should also know to never remove or deface a container label.
Each laboratory or shop area using chemicals must have ready access to the appropriate supplies needed to handle a spill. Safety data sheets (formerly material safety data sheets) can provide details to determine which items may be necessary for the particular chemicals in your area. Refer to your chemical list or review the chemicals actually in use (standard operating procedures) for laboratories to determine what items are needed.
A typical lab kit might include:
- Mercury absorb sponges;
- Sorbents appropriate for chemicals present (e.g., kitty litter, spill pads, vermiculite);
- Neutralizers; and
- Dust pan / broom (non-metal).
Generally spill cleanup materials can be purchased from most scientific and safety supply vendors. Please contact 540-231-3427 for additional information as needed.
Labs working with infectious biological material must have access to a spill kit which should contain the following:
- PPE appropriate for the material (e.g., gloves, tyvek coveralls, booties, N-95 respirator, eye protection);
- Autoclavable biohazard bags;
- Disinfectant (e.g., chlorine bleach -10,000ppm);
- Absorbent material such as paper towels or pads;
- Forceps or brush and dust pan to pick up sharps; and
- Sharps container.
These items can be purchased (like for chemical supplies) from most scientific and safety supply vendors. For questions, please call 540-231-3361.
For information regarding radiological spill supplies, please contact 540-231-5364.
University personnel using hazardous materials in their research and/or teaching laboratories, or any other space where chemicals are used/stored must generate an inventory listing and update it annually. This policy resulted from negotiations with the State Fire Marshall related to chemical use and storage, and concerns raised by accidents at other universities as well as the Federal Bureau of Investigation. The registration process has been vetted through the University Environmental Health and Safety Committee as well as the Chemical Safety and Hazardous Materials Management Committee, and the Occupational Health and Safety Committee.
Registration is completed through the Safety Management System. For additional information, please contact Zack Adams, 540-231-5985.
If a lab only uses chemicals and/or radioisotopes, then a designated area within the lab may be used for storage and consumption of food and drink. If the lab uses ANY biological material, then no food or drink is allowed in the lab and storage and consumption of food and drink must occur in a designated area OUTSIDE of the laboratory.
Review the information contained on the safety data sheet. If one is not available, you may contact the manufacturer, importer, or supplier to request one. If you still need assistance, please contact 540-231-3600.
Documents
Contact Information
Autumn Timpano, University Chemical Hygiene Officer
Phone: 540-231-3427
Email: actimpano@vt.edu