Electrical Safety in Research Operations
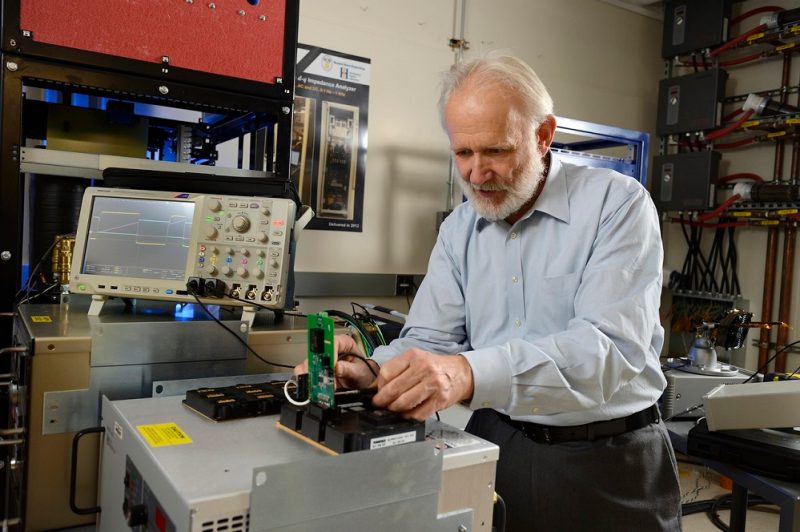
This program establishes requirements for personnel performing electrical research.
Electrical Safety for Research Program
Risk Assessment Process and Work Controls
Risk assessment for electrical research operations at Virginia Tech is based upon the Department of Energy's Handbook 1092-2013 and NFPA 70E-2021 (for traditional electrical hazards). There are hazard classification charts to cover 60 Hz, DC, capacitors, batteries, sub-RF, and RF power sources. It is possible that a system has more than one energy source. Hazard classification charts are available in the DOE handbook and are provided during Environmental Health and Safety Electrical Safety for Research training. Charts and tables for more traditional electrical work are available in Environmental Health & Safety's Electrical Qualified Person training. Depending on the nature of the research project, both trainings may be beneficial.
Students, in conjunction with their professor and/or Lab Manager, should determine the hazard class for each power source present in the research apparatus. The hazard class will then be used to determine appropriate guidance for the mode of operations being performed at any given time.
Refer to the various thresholds listed in this section. If the thresholds are crossed, appropriate hazard controls and/or personal protective equipment will be necessary as defined per the hazard class.
Threshold Requirements
If an electrical shock or arc flash threshold is exceeded (by the design of the system/equipment/components) or crossed by personnel in proximity to exposed, energized electrical component, hazard controls must be implemented to eliminate or reduce exposure to an acceptable level. Where the risk cannot be eliminated or reduced to an acceptable level, electrical personal protective equipment must be selected for the voltage and incident energy expected and worn by qualified personnel who are working within the approach boundaries.
Electrical Shock Thresholds
In research and development, conditions and controls found in a typical electrical system may be temporarily removed or not within the scope of the project. For example, covers and barriers may be removed from energized systems exposing personnel to a shock hazard. Electrical shock can be fatal. The following thresholds for defining shock hazards are to be observed in research and development applications.
- AC (60 Hz): greater than 50 volts and greater than 5 mA
- DC (all): greater than 100 volts and greater than 40 mA
- Capacitors (all): greater than 100 volts and greater than 1 J, or greater than 400 volts and greater than 0.25 J
- Batteries (all): greater than 100 volts
- Sub-RF (1 Hz - 3 kHz): greater than 50 volts and greater than 5 mA
- RF (3 kHz - 100 MHz): a function of frequency
Arc-flash Thresholds
Arc flash burns may be caused by electric arcs, and are similar to any other heat burn; however, arc-blast hazards (at much greater energy potential resulting in serious injury or death) may be present during research and development applications. Arc-blasts occur rapidly and can result in significant injury or death, as well as equipment destruction. The following arc-flash thresholds are to be observed in research and development applications.
- AC (60 Hz):
- Less than 240 volts and the transformer supplying the circuit is rated greater than 125 kVA
- Less than 240 volts and the transformer supplying the circuit is supplied by more than one transformer
- Greater than 240 volts
- DC (all): greater than 100 volts and greater than 500 amps
- Capacitors (all): greater than 100 volts and greater than 10 kJ
- Batteries (all): greater than 100 volts and greater than 500 amps
- Sub-RF (1 Hz - 3 kHz): greater than 250 volts and greater than 500 amps
- RF: N/A
Approach Boundaries
When these boundaries are crossed, hazard controls appropriate for the risk category must be implemented. Risk categories are determined via tables and charts provided in DOE-HDBK-1092-2013, Appendix D. This information is covered during training. Risk categories include: "no hazard, "little to no hazard," "injury or death could occur by close proximity or contact," "injury or death could occur by proximity or contact," or a "high level of risk where significant engineering and administrative controls are necessary to manage the hazard."
In addition to proper electrical training, the following controls may be required to eliminate or significantly reduce the associated risks with electrical research activities.
Isolation/distance
Isolation and distance can eliminate potential exposure to electrical hazards, or reduce the risk to an acceptable level. These options should always be considered when the threshold is reached or exceeded. Examples of isolation and distance include:
- Control rooms designed for electrical apparatus testing when the potential risk is significant;
- Shielding;
- Personnel located outside of approach boundaries; and/or
- Remote sensors and testing/diagnostic equipment.
Two-person rule
Higher risk energized work may require a second person to be present, known as the "two-person rule" or "buddy system." The second person must also be "qualified," and must understand the work activities and hazards present. This person must be trained to know what to do in case of an electrical incident involving the other worker, including the location of electrical disconnects, information for contacting emergency services, and first aid/CPR/AED response.
Safety watch
In some instances, a "safety watch" is necessary. The use of a safety 2atch is more stringent than the two-person rule. Safety watch responsibilities and qualifications include:
- Training in methods of the release of victims from contact with electrical energy, cardiopulmonary resuscitation (CPR), and the use of automated external defibrillators (AED);
- Thorough knowledge of location and operation of emergency shutdown push buttons and power disconnects;
- Thorough knowledge of the specific working procedures to be followed and the work to be done;
- Monitoring the work area for unsafe conditions or work practices, and taking necessary action to ensure abatement;
- De-energizing equipment and alerting emergency rescue personnel as conditions warrant;
- Maintaining visual and audible contact with personnel performing the work;
- Removal of injured personnel, if possible;
- Preventing unqualified persons from crossing the established safe approach boundaries; and
- No other duties may preclude observing and rendering aid.
Standard Operating Procedures
Work controls, as recommended in the risk assessment, may include documented standard operating procedures (SOP) for hazardous electrical research work. The SOP should include specific steps to be taken in order to energize the apparatus, run the test, and de-energize the apparatus. It should also include the results of the risk assessment, including the hazard class, controls to be implemented for modes of operation involving a potential exposure to electrical hazards, approach boundaries, and specific personal protective equipment to be worn. A schematic of the system should be included, which identified the various components and their magnitudes (voltages, pressures, temperatures, etc.). Documentation from the department regarding reviews and approvals must be made available upon request.
Energized Electrical Work Permit
An Energized Electrical Work Permit (EEWP), or equivalent written approval from the lab manager/principal investigator, must be completed and approved where the task is not specifically exempt from written approval (e.g. voltage-testing or diagnostics), and where the system must be energized and approach boundaries will be crossed. Work performed under energized conditions is generally prohibited, but may be considered where a power source physically cannot be de-energized (i.e. batteries). Elimination (of the electrical hazard to personnel) and engineering controls must be considered and implemented, where feasible before energized work is approved by three levels of management and permitted.
Electrical Personal Protective Equipment
Whenever electrical tasks are being performed, including voltage testing, where the approach boundaries will be crossed, appropriate electrical personal protective equipment must be provided by the department and worn by personnel.
Contact Information
Robin McCall-Miller, Occupational Safety Program Manager
- Call: 540-231-2341
- Email: rmmiller@vt.edu