Machine Shop Safety
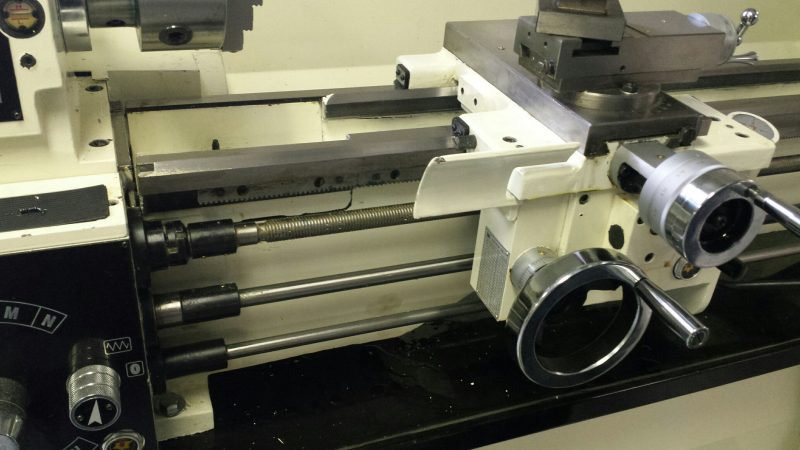
Machine Shop Safety Quick Links
Machine Shop Safety Program
Machinery Hazards Overview
Machinery and equipment may have the following hazards which require controls to be in place:
- Point of operation: Refers to the area where work (e.g. cutting, shearing, shaping, boring) is performed on a stock material. Some machinery, such as table saws and bandsaw have a point of operation guarding that must be in place during operation.
- Nip or pinch point: Refers to an area other than a point of operation where a belt contacts a pulley or one or more rotating parts come together where it is possible for a part of the body to get nipped or pinched by the moving parts. Machinery with rollers is a prime example of nip/pinch points.
- Power transmission: Refers to areas where power is transferred from one part to another such as a drive shaft, belt, or chain. Belts, pulleys, flywheels, rotating parts, etc. must be guarded to prevent entanglement and amputations. Older machinery is notorious for not providing this type of guarding.
Operator's Manual/Manufacturer's Instructions
The owner's or operator's manual must be in the shop area with the machine.
Standard Operating Procedures (SOP)
A standard operating procedure indicating safety features and their appropriate use may be necessary for more complicated machinery. Some machinery may require operating steps be performed in a certain manner. SOPs define these criteria and should be used for training personnel prior to use.
Space About Machinery
- The area of operation must be free and clear of obstructions.
- Slipping hazards (e.g. oil or debris) in front of machinery should be addressed with appropriate mats.
- Space must be provided between each machine and other objects, including other machine operating areas, as needed, to allow the safe operation of the machine. A good rule of thumb is three feet.
- Adequate space for feeding stock into machinery must be provided.
- Machinery must not obstruct access to electrical disconnects.
Guarding
One issue with older shop equipment is that it may not have appropriate guarding when compared to newer standards and design requirements. Machine guarding issues are not grandfathered by OSHA and must be addressed before the machine is used. Check with the manufacturer first to see if a retrofit kit is available. If so, it will be up to the department to purchase and install it. If a retrofit kit is not available, a guard may have to be manufactured and installed. In general, the guard must sufficiently cover the hazard without creating an additional hazard. EHS can provide general recommendations, if necessary.
Out-of-service or Out-of-order
Machinery that is no longer used by a department should be removed from the site. Older machinery typically has insufficient guarding or other issues that would prohibit safe use and must be secured by a positive means to prevent accidental use while it remains onsite. "Positive means" would include placing a "Do Not Use" tag on the machine that specifies the problem (ex. missing guard) and applying an energy isolating device and lock on the cord-and-plug, or cutting the plug off of the machine to prevent someone from using the machine easily.
Machinery and equipment must be inspected and maintained according to the manufacturer's recommendations. This information, along with safety-related guidelines, can be found in the operator's manual. If a manual is not available, the manufacturer should be contacted to obtain one. Many manufacturers post manuals on their websites.
Hazard Controls
Many control systems exist to provide protection from hazards. Users must be provided protection from all hazards during their work in a machine shop.
Engineering controls must be given first priority. If engineering controls are not feasible, then an appropriate administrative control must be used. If administrative control will not control the hazard, then personal protective equipment must be utilized by the machine user.
Engineering controls include machine guarding, ventilation systems, and dust collection systems.
Machine guarding
There are three main types of guards. At least one type of guard can provide protection from most machine hazards.
Fixed guard refers to a guard that is a permanent part of the machine, but is not dependent upon moving parts of the machine to perform its guarding function. A fixed guard that can be manually set into the appropriate position before machine operation is sometimes referred to as an adjustable guard. A fixed guard that completely separates the user from the hazard is often called an"enclosure guard.
Interlocked guard refers to guards that are connected to a mechanism that cuts power to the machine when the guard is tripped or moved out of position.
Self-adjusting guard refers to a guard that adjusts automatically to the thickness and movement of the stock material. An example is a floating guard on a table saw that raises up and floats along the top of the stock while the stock is guided across the saw.
Ventilation systems
When chemical or flammable liquid work, welding operations, or soldering is performed additional ventilation may be required. This may include fume hoods, ventilation hoods, or local exhaust ventilation systems.
Dust collection systems
Dust collection systems remove sawdust or other particles from the shop area. The particulates are generally collected in a bag or other container for disposal. Where woodworking or other dust generation activities are conducted, it is recommended that a dust collection system be put in place.
Administrative controls may be necessary when engineering controls are not available or feasible. Such controls include:
- Safety training
- Machine-specific operation training (required)
- Manufacturer's instructions/operator's manual review
- Standard operating procedures
- Machinery and shop layout
- Restricted access
- Preventative maintenance
- Established shop guidelines or policy
- Signage, barriers, or other warning methods
Personal protective equipment used in a machine shop may include safety glasses, protective shoes, face shields, respirators, gloves (typically for material handling only - not recommended during machine use in many instances), welding gear and disposable clothing. Hazards in the shop area and for tasks performed must be evaluated and controlled. Where personal protective equipment is required, it should be documented on a Hazard Assessment Form and personnel using such equipment must be trained. For more information regarding recommendations and guidelines for requiring specific personal protective equipment, review the Personal Protective Equipment Program.
Frequently Asked Questions
Yes, Virginia Tech can be cited by Virginia OSHA (VOSH) and penalties can be assessed. Any violation cited must be abated within the specified period, or contested. Penalties will be the responsibility of the cited department. Environmental Health & Safety coordinates the response efforts. Contact Environmental Health & Safety (Robin Miller) at 540-231-2341 or 540-231-5985 (Zack Adams) for assistance.
Regardless of who owns the equipment or tools used by an employee while on the job, it must be in good condition and in proper working order. Good condition would also include any required safety features of the equipment/tool. Departments permitting employee-owned equipment/tools to be used while on the job are responsible for ensuring it is safe. If the person is injured while on the job because of defective, improper, or sub-standard equipment, it is still work-related. It is our goal, and everyone's obligation, to reduce hazardous conditions in the workplace.
All program requirements still apply; however, shop policies and designated coordinators may not be necessary for such limited applications.
Hoists typically only offer two directions of load motion: forward/reverse and up/down. Cranes typically offer three directions of load motion: forward/reverse, up/down, and left/right.
Also look at what the manufacturer calls it, as well as any design and installation drawings.
Hoists are typically mounted on a beam, which must be rated with a load capacity that is equal to, or greater than, the rating on the hoist.
Documents and Resources
Above Ground Storage Tanks (ex. fuel tanks)
Boiler and Pressure Vessels (ex. air compressors)
Personal Protective Equipment Program
Welding/Cutting/Brazing/Soldering
Contact Information
Robin McCall-Miller, Occupational Safety Program Manager
Phone: 540-231-2341
Email: rmmiller@vt.edu