Lockout/Tagout
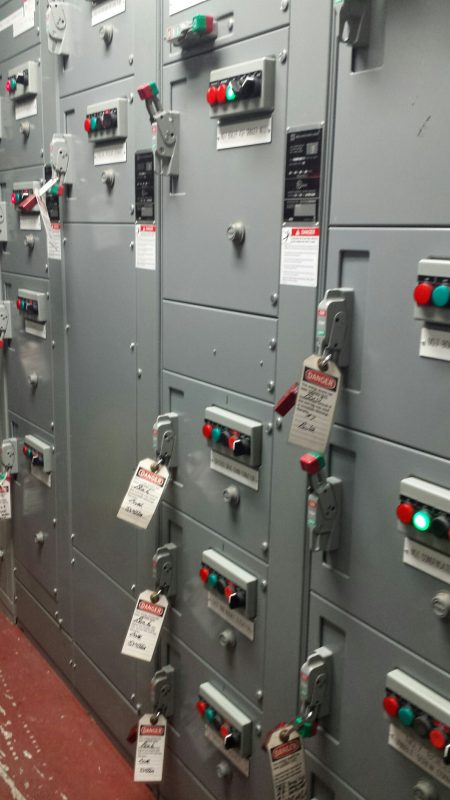
Lockout/Tagout Quick Links
The Lockout/Tagout Program defines procedures for the control of hazardous energy sources in order to prevent injuries during the service or maintenance of machinery or equipment.
Lockout/Tagout Program
Frequently Asked Questions
No. See definitions above for energy isolating devices.
No. Voltage pens (i.e. non-contact test equipment) may not always detect the presence or absence of voltage due to design and use limitations. They may be useful in some applications, or as a secondary means of verification. Always review the manufacturer's instructions for proper use and restrictions.
No, only those that have more than one energy type, more than one energy source, or more than one energy form (i.e. active and stored) require and ECP. Equipment similar in nature and operation (ex. air compressors) may be covered under one ECP.
No, not if fluid is being prevented from flowing into space in this manner. Two in-line valves are required for "elimination" of the hazard.
Yes, if the hydraulic energy is the source of power to drive or activate a device within a space.
Yes, as long as the guarding method chosen effectively protects the entrant.
Yes.
Only if the pipe is blanked or blinded, misaligned or section removed, or double blocked and bled.
Is training mandatory? If so, when? Yes. Any person who is to perform work on energized electrical or mechanical systems must attend this training.
Class length: 3 hours.
Available online: No.
When is refresher training required? Every 3 years.
Please see the online class schedule for more information.
Is training mandatory? If so, when? Yes. it's required for those persons who work around lockout situations but are not authorized to apply locks. General awareness training on the requirements of this program is available upon request.
Class length: 1 hour
Available online: Yes
When is refresher training required? Every 5 years.
Please see the online class schedule for more information.
A device used to ensure the continuity of energy isolation during a multi-shift operation. It is placed on a lockbox. The key to the job lock is controlled by the assigned primary authorized employee for the job, or transferred from one to another if responsibility changes from shift to shift.
A mechanical device that physically prevents the transmission or release of energy, such as manually operated electrical circuit breakers, disconnected switches, manually operated switches by which the conductors of a circuit can be disconnected from all ungrounded supply conductors and no pole can be operated independently, a line valve, a block, and any similar device used to block or isolate energy.
Constructing, installing, setting up, adjusting, inspecting, modifying, troubleshooting, lubrication, cleaning, unjamming, tool adjustments, tool changes (where the employee may be exposed to the unexpected energization or startup of the equipment or release of hazardous energy).
Using the machine/equipment to perform its intended production function. Tasks are routine, repetitive, and integral to the production.
- Electrical greater than 50 volts
- Mechanical that can result in injury
- Hydraulic greater than 12 psi
- Pneumatic greater than 12 psig
- Gravity that can result in injury (impact, pinch point)
- Chemical that can result in injury (burn, acute inhalation hazards)
- Thermal that can result in injury (2nd degree burn or worse)
Locks, chains, valve protectors, self-locking fasteners, blanks that use a positive means to hold an energy isolation device in a safe position and prevent energization of the machine/system.
In group lockout/tagout situations, it's the authorized person who exercises overall responsibility for adherence to the employer’s lockout/tagout procedure.
An authorized person who oversees or leads a group of serve/maintenance workers.
This would be a machine operator, for example, who does not perform servicing/maintenance on it, or a person who works in an area where lockout/tagout is being performed. Affected persons need to understand the requirements of the program so that they do not override the procedures which could result in a maintenance employee injury.
A person who locks/tags out machines or equipment in order to perform servicing or maintenance on that machine/equipment.
Before performing any servicing or maintenance on a machine or equipment where the unexpected energizing, startup, or release of stored energy could occur and cause injury.
If workers do not have an accurate map (i.e. one-line diagram) of the electrical system, they can be exposed to potential back feeds from alternate sources, energized capacitors, undocumented switching conditions, and unknown voltages, in addition to the problem of not being able to accurately perform lockout/tagout procedures.
Source: "Compliance Takes More Than a Label," Facility Safety Management, January 2008, Chet Davis
Documents
Contact Information
Robin McCall-Miller, Occupational Safety Program Manager
Phone: 540-231-2341
Email: rmmiller@vt.edu