Silica Exposure Control Plan
Silica Awareness Quick Links
This is an example of the type of work that can produce respirable crystalline silica.
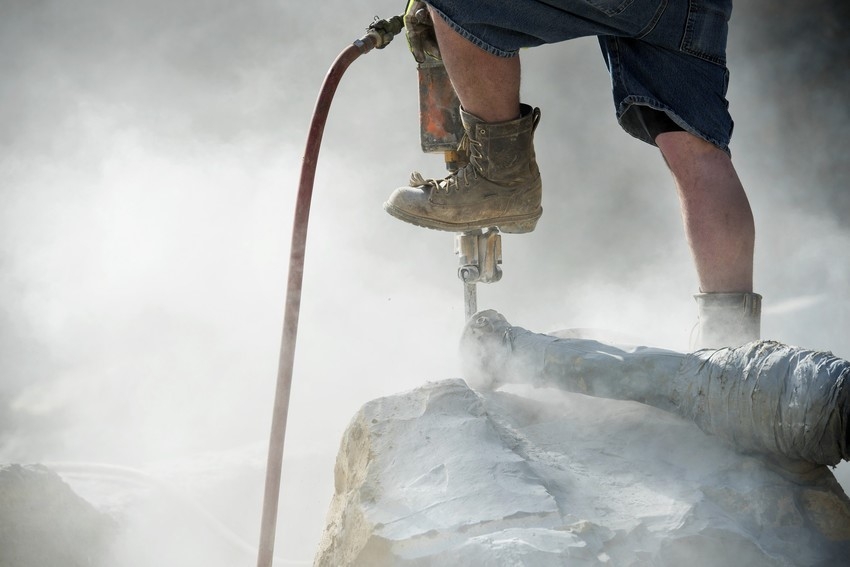
Some types of research can produce respirable crystalline silica
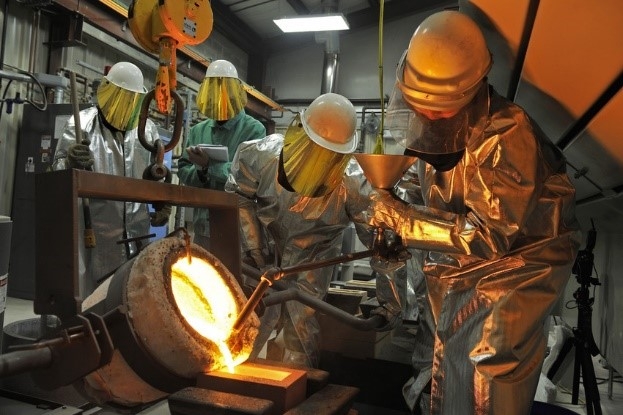
Application
The Silica Exposure Control Plan (SECP) applies to all university operations where personnel could be exposed to respirable crystalline silica (RCS) above the limits established by OSHA. The purpose of this program is to assure appropriate controls are used to maintain exposures below these limits whenever feasible, that persons covered by this program are informed of the hazards of RCS exposure, and that employees exposed above limits are provided required medical services. RCS can be created by crushing, drilling, grinding, cutting, sanding, or abrading certain types of materials such as sand, stone, mortar and concrete, porcelain and ceramic materials, brick and pottery products, plaster and sheetrock compounds, and refractory materials. RCS may also be found in the clay body and glazes of pottery, released during jewelry production, used in foundries, and may be released when mining, excavating, or otherwise disturbing the earth's surface.
Operations that use crystalline silica or work which affects materials containing silica where respirable dust could be generated must comply with this program. Departments that perform renovation, repair, or maintenance activities that could affect potential silica-containing materials shall designate a responsible person to coordinate program requirements in the department with EHS.
The Silica Exposure Control Plan (SECP) is administered by Environmental Health and Safety. Departments who perform construction, renovation, maintenance, or repair activities that affect building or other materials potentially containing silica, and from which respirable dust could be generated, shall designate a Safety Representative to coordinate the requirements of this program in the department. All other departments that have work operations that use or create respirable crystalline silica (RCS) shall comply with the requirements outlined in this program.
Departments
Departments performing construction, renovation, maintenance, or repair work covered by this section shall:
- Designate a safety representative to coordinate monitoring, evaluations, and training with Environmental Health & Safety, and to provide oversight on departmental operations to determine when work activities may generate RCS that will require review by Environmental Health & Safety.
- Ensure the work practices and procedures used to control exposure to RCS comply with this program.
- Ensure all reasonable precautions are taken to prevent exposure of bystanders and the general public when work involving RCS is performed.
- Ensure covered employees attend required training, and participate in the Occupational Health Assurance Program if required.
All other departments performing work where RCS may be created or released shall coordinate with EHS to have the work activity reviewed and air monitoring performed as necessary. RCS can be created by crushing, drilling, grinding, cutting, sanding or abrading certain types of materials such as sand, stone, mortar and concrete, porcelain and ceramic materials, brick and pottery products, plaster, sheetrock compounds, and refractory materials. RCS may also be found in the clay body and glazes of pottery, released during jewelry production, used in foundries, and may be released when mining, excavating or otherwise disturbing the earth surface. Where exposures of concern are identified by Environmental Health & Safety, EHS will work with the department to develop and implement a worksite‐specific Exposure Control Plan.
Designated departmental safety representatives are responsible for the following:
- Notifying EHS when work activities are planned that may generate RCS where monitoring may be required. Employee exposure monitoring is not required if a task is listed in the Specified Exposure Control Methods (SECM) section of this program and the engineering controls, work practices and PPE are used as listed.
- Working with supervisors to review all power tools used to assure compliance with the dust controls established in the SECP. Where respirators are required by the SECP, assure supervisors only allow employees who have been approved to use respirators within the past twelve months to perform those tasks.
- Assuring regulated areas are established, dust controls are used to prevent migration of dust from the worksite, and air supply and returns in the work area are covered when work will be performed near areas occupied by the general public and respiratory protection is mandated in the SECM.
Supervisors
Supervisors shall:
- Ensure all employees who perform work that may generate RCS have attended Silica Awareness Training.
- Implement and ensure procedures are followed in accordance with this Plan.
- Ensure that staff are aware of this Plan, instructed on the details of implementation, and provided with the equipment and methods of control (e.g. engineering controls, work practice controls and respirators) outlined in the SECM.
- Assure only employees who have been medically cleared by EHS are allowed to use respirators.
- Notify Environmental Health & Safety when a task must be performed that is not covered in the SECM and where no prior exposure monitoring has been performed.
- Contact Environmental Health & Safety to request technical assistance, and to evaluate health and safety concerns within their department.
Employees
Employees shall
- Comply with this Plan and any further safety recommendations provided by supervisors and/or EHS regarding the Silica Exposure Control Plan.
- Contact the supervisor or Environmental Health & Safety to request technical assistance, and to evaluate health and safety concerns within their department.
Environmental Health & Safety
Environmental Health & Safety will provide technical support, employee exposure monitoring, and oversight for this program; however, involvement by Environmental Health & Safety does not relieve the departments, supervisors, or contractors of their individual responsibilities. EHS responsibilities for this program include:
- Developing, implementing, and administering the Silica Exposure Control Plan, including delineation of responsibilities and standardized work procedures (SWP).
- Providing awareness level for all employees performing work that may generate RCS, and maintaining centralized training records.
- Providing respiratory protection training and fit-testing for employees.
- Serving as a technical resource for program applications on campus.
- Performing employee exposure monitoring, documenting the level of exposure to RCS for various tasks, and updating the SECP to include these new tasks along with required PPE.
Contractors
Contractors shall comply with the Safety Requirements for Contractors and Subcontractors Program.
Program Requirements
Initial exposure assessment
Exposure monitoring will be conducted when any employee is or may reasonably be expected to be exposed to respirable crystalline silica at or above the action level. Exposure monitoring may also be performed if work covered by this program is being performed near areas occupied by the general public where respiratory protection is required by the SECM, and where other appropriate dust controls cannot be employed.
Employee exposure monitoring is not required if the task is listed in the SECM section of this program and the engineering controls, work practices, and PPE are used as listed. Exposure monitoring is also not required if EHS has either objective or historic data that shows employees will not be exposed above limits for the task being performed. If a department purchases tools not listed in the SECM that incorporate dust controls, notify EHS so we can obtain their objective data on the effectiveness of the dust controls.
If a task needs to be performed that is not outlined in the SECM section of this program, please contact Environmental Health & Safety for assistance.
Periodic exposure assessment
If the most recent results are at or above the action level but are below the permissible exposure limit (PEL), monitoring will be repeated every 6 months.
If the most recent results are at or above the PEL, monitoring will be repeated within 3 months.
Periodic exposure monitoring may be discontinued if results from two consecutive sampling periods taken at least 7 days apart show that employee exposure is below the action level.
Monitoring will be conducted whenever a change in the production, process, control equipment, personnel, or work practices may reasonably be expected to result in new or additional exposures at or above the action level.
Employee notification
Employee(s) will be notified in writing of the results of the assessment within 15 workdays or the results will be posted in an appropriate location accessible to all affected employees.
If the result is above the PEL, the notification will include the means that are being taken to reduce the exposure to below the PEL.
A regulated area will be established where work exposures at a fixed location are known to be at or above the PEL on a consistent basis. A temporary restricted area will be established where the task is covered in the Specified Exposure Control Methods section of this program and the task will not be performed regularly in the same area or location.
A regulated area must be separated from other areas in a way that will minimize the number of employees exposed. The following sign will be posted at each entrance to the regulated area:
DANGER
RESPIRABLE CRYSTALLINE SILICA
MAY CAUSE CANCER
CAUSES DAMAGE TO LUNGS
WEAR RESPIRATORY PROTECTION IN THIS AREA
AUTHORIZED PERSONNEL ONLY
Only employees who have work to perform are allowed to enter a regulated area. All employees entering the regulated area must wear a respirator, regardless of the amount of time spent in the area. Air from a regulated area shall not be recirculated by the building ventilation system unless it is first cleaned by HEPA filtration.
Tasks performed in accordance with the SECM and where respirators are required for the task shall be performed in a temporary restricted area. A temporary restricted area shall be designated by signs, barriers, or other effective means that will assure unauthorized persons do not enter. Where these tasks are performed near areas occupied by the general public, dust barriers shall be installed as needed to prevent dust migrating into those areas. If a building ventilation system provides air to the area where restricted work is being performed, the air returns from that system shall be blanked or closed while that work is in progress.
Where tasks are performed indoors or in an enclosed area, exhaust shall be provided as needed to minimize the accumulation of visible airborne dust. If this exhaust is vented inside the building, or outside in an area where the public may be exposed, the exhaust system must incorporate HEPA filtration. For tasks performed using wet methods, water shall be applied at a rate that is sufficient to minimize the release of visible dust.
When tasks are performed in accordance with this program and the SECM are followed, this program will serve as the Written Exposure Control plan.
For fixed worksites where exposures above the action level occur on a routine basis, a worksite-specific written exposure control plan must be developed. Please contact EHS for assistance with writing your plan. The plan must be reviewed at least annually.
If a task must be performed that is not addressed by the SECM, exposure monitoring must be performed and a worksite-specific or task-specific exposure control plan must be developed. Please contact EHS for assistance with evaluating the task(s) and writing the plan.
Engineering and work practice controls
For any work task or work location where the exposure to RCS is above permissible limits, engineering controls (i.e. wet work, ventilation) or work practice controls (i.e. housekeeping, inspections, scheduling) will be implemented to lower the exposure as much as possible.
Housekeeping
Dry sweeping or dry brushing of dust containing respirable crystalline silica is not allowed. Instead, use a HEPA filtered vacuum cleaner, followed by wet mopping or wet sweeping as necessary.
Do not use compressed air to clean an employee’s clothes that have become soiled with dust containing respirable crystalline silica. Rather, use a HEPA filtered vacuum to remove dust followed by laundering.
Medical services
Any employee who is exposed above the action level for 30 or more days per year will be provided a medical evaluation and other required medical services at no cost. The medical evaluation is performed initially and at least every 3 years, unless the Occupational Physician requires a more frequent review. If respirators need to be worn by an employee, the employee must be medically cleared, fitted to the respirator and trained annually by Environmental Health & Safety.
The medical evaluation will include medical and work history, a physical exam, chest x-ray, pulmonary function test, tuberculosis test, and any other test recommended by the Occupational Physician.
Hazard communication
Silica must be included in each department’s hazard communication program as applicable. This includes proper labeling and having a Safety Data Sheet (SDS).
Training
Any employee who is exposed to silica above the action level is required to complete a silica safety training course on an annual basis.
Departmental reviews
Each department shall review its written exposure control plan on an annual basis. The review shall consist of determining if the task and controls are still being used as described and if the plan is effective in reducing silica exposure.
Environmental Health & Safety audits
Environmental Health & Safety will audit each department that has an Exposure Control Plan on a yearly basis. The audit will cover all aspects of the written program to ensure they are up to date and complete. The audit will also include a walkthrough of the area to check for appropriate labels, warning signs, and housekeeping.
Specified Exposure Control Methods
For each employee working with materials containing crystalline silica and engaged in a task using the equipment and machines listed below, the supervisor shall assure the engineering controls, work practices, and respiratory protection are used as specified. In all cases, be sure to operate and maintain the tool in accordance with the manufacturer’s instructions to minimize dust emissions. If the designated engineering controls are not available, or if the task is not listed below, do not begin the work and contact EHS for guidance.
Engineering control: Saw equipped with integrated water delivery system that continuously feeds water to the blade.
Respiratory protection: None required.
Engineering control: Saw equipped with integrated water delivery system that continuously feeds water to the blade
Respiratory protection:
- Enclosed area: Can Not Use Saw Inside or in Enclosed Areas.
- Outside area: None Required.
Engineering control: Saw equipped with integrated water delivery system that continuously feeds water to the blade.
Respiratory protection (less than 4 hours per shift):
- Enclosed area: N95 respirator.
- Outside area: None required.
Respiratory protection (more than 4 hours per shift):
- Enclosed area: N95 respirator.
- Outside area: N95 respirator.
Engineering control: Task may only be performed outdoors. Saw equipped with commercially available dust collection system equipped with HEPA filtration.
Respiratory protection: None required.
Engineering control: Saw equipped with integrated water delivery system that continuously feeds water to the blade.
Respiratory protection (less than 4 hours per shift):
- Enclosed area: N95 respirator.
- Outside area: None required.
Respiratory Protection (more than 4 hours per shift):
- Enclosed area: N95 respirator.
- Outside area: None required.
Engineering control: Tool equipped with integrated water delivery system that supplies water to the cutting surface.
Respiratory protection: None required.
Engineering control: Commercial shroud or cowling with HEPA filtered dust collection system
Respiratory protection: None required.
Engineering control: Commercial shroud or cowling with HEPA filtered dust collection system.
Respiratory protection (less than 4 hours per shift):
- Enclosed area: Cannot use drill in enclosed areas.
- Outside area: N95 respirator.
Respiratory Protection (more than 4 hours per shift):
- Enclosed area: Cannot use drill in enclosed areas.
- Outside area: N95 respirator.
Engineering control: Use HEPA filtered dust collection system with close capture hood – OR – Shroud around drill bit with a low-flow water spray to wet the dust at the discharge point from the dust collector – OR – Operate from within an enclosed cab and use water for dust suppression on drill bit.
Respiratory protection: None required.
Engineering control: Water continuously fed to the point of impact – OR – commercial shroud or cowling with HEPA filtered dust collection system.
Respiratory protection (less than 4 hours per shift):
- Enclosed area: N95 respirator.
- Outside area: None required.
Respiratory protection (more than 4 hours per shift):
- Enclosed area: N95 respirator.
- Outside area: N95 respirator.
Engineering control: Water continuously fed to the point of impact – OR – commercial shroud or cowling with HEPA filtered dust collection system. When used indoors or in an enclosed area, use a HEPA-filtered vacuum to remove loose dust in between passes.
Respiratory protection: None required.
Engineering control: Use a machine equipped with supplemental water sprays designed to suppress dust. Water must be combined with a surfactant.
Respiratory protection: None required.
Engineering control: For cuts of any depth on asphalt, or cuts of four inches in depth or less on any material, use a machine equipped with exhaust ventilation on drum enclosure and supplemental water spray designed to suppress dust. – OR – use a machine equipped with supplemental water spray designed to suppress dust. Water must be combined with a surfactant.
Respiratory protection: None required.
Engineering control: Use equipment designed to deliver water spray or mist at crusher and other points where dust is generated. – AND – use a ventilated booth that provides fresh, climate-controlled air to the operator, or a remote control station.
Respiratory protection: None required.
Engineering control: Operate equipment from within an enclosed cab. – AND – When employees outside of the cab are engaged in the task, apply water and/or dust suppressants as necessary to minimize dust emissions.
Respiratory protection: None required.
Engineering control: Apply water and/or dust suppressants as necessary to minimized dust emissions. – OR – when the equipment operator is the only employee engaged in the task, operate equipment from within an enclosed cab.
Respiratory Protection: None required.
Engineering control: Grinder equipped with commercial shroud and HEPA filtered dust collection system. Dust collector must provide 25 cubic feet per minute or greater of airflow per inch of wheel diameter.
Respiratory protection (less than 4 hours per shift):
- Enclosed area: N95 respirator.
- Outside area: N95 respirator.
Respiratory protection (more than 4 hours per shift):
- Enclosed area: Full face air purifying respirator.
- Outside area: Full face air purifying respirator.
Engineering control: Tool equipped with integrated water delivery system that supplies water to the grinding surface – OR – grinder equipped with commercial shroud and HEPA filtered dust collection system
Respiratory protection (less than 4 hours per shift):
- Enclosed area: None required.
- Outside area: None required.
Respiratory Protection (more than 4 hours per shift):
- Enclosed area: N95 respirator.
- Outside area: None required.
Contact Information
Zack Adams, Assistant Director, Occupational Safety and Health Programs
Phone: 540-231-3600
Email: adamsz@vt.edu